Magnetic Levitation Bearing System
20% error reduction in high-speed rotational systems
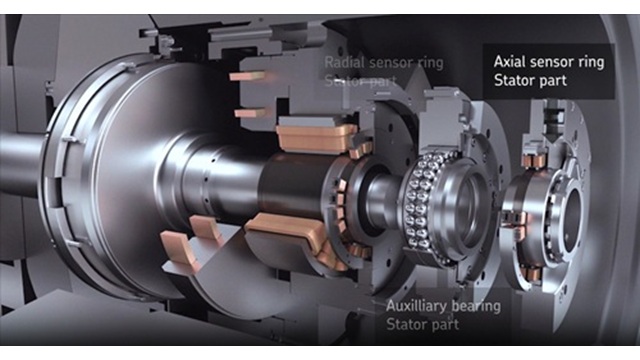
Project Overview
Designed and tested mechatronic systems including rotary magnetic levitation bearings for high-speed industrial applications. The system was developed to provide contact-free rotation with minimal friction and wear for wafer manufacturing systems.
Key Challenges
- Precision alignment requirements for micron-level tolerances
- Thermal management in high-speed operation
- Vibration control and dynamic balancing
- Integration with existing manufacturing systems
Design Process
Requirements Analysis
Collaborated with electrical engineers to define magnetic field requirements, load capacities, and rotational speed parameters. Developed specifications for radial and axial clearance tolerances.
Prototype Development
Created multiple prototype configurations in SolidWorks evaluating different permanent magnet and electromagnetic arrangements. Conducted preliminary FEA on magnetic flux distribution.
Testing & Validation
Performed rotational testing at speeds up to 20,000 RPM, measuring vibration amplitudes and temperature rise. Conducted accelerated life testing to validate bearing durability.
Production Implementation
Developed detailed fabrication drawings with GD&T per ASME Y14.5. Created assembly procedures and quality control checkpoints for manufacturing.
Results & Impact
Technical Specifications
Materials
- Neodymium permanent magnets (N52 grade)
- Stainless steel 316 for non-magnetic components
- High-temperature epoxy for coil encapsulation
Performance
- Max speed: 20,000 RPM
- Radial load capacity: 500 N
- Axial load capacity: 200 N
- Operating temperature: -20°C to 120°C
Design Features
- Active position sensing
- Fail-safe mechanical backup
- Integrated cooling channels
Design Visualizations
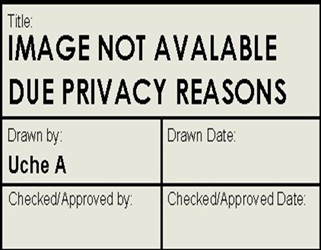
Bearing Assembly
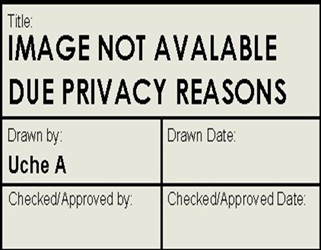
Magnetic Flux Analysis
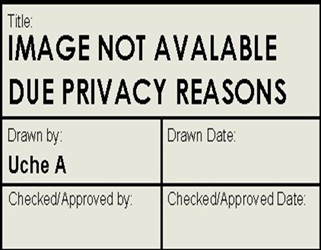
Production Unit